Process engineering references
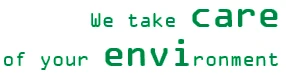
Processing of gas-forming metal-containing residues
Client : Austrian industrial company
Period : 2020
Services : Feasibility study and planning and monitoring of laboratory and pilot tests
Metal-containing waste with an excessive gas formation potential must be conditioned at great expense before it can be landfilled at low cost. If water is added in the process, considerable gas emission occurs in some cases, which has a relevant energy content due to the high hydrogen concentration. This is to be utilised thermally or electrically at the existing operating locations.
Based on orienting laboratory tests, various plant concepts were first roughly designed and economically evaluated in a feasibility study. Subsequently, pilot tests were carried out, which showed that with various metal-containing residues, the addition of water not only resulted in strong gas formation, but also that this gas was very rich in hydrogen and therefore excellent for further uses.
Risk assessment based on §59 AWG
Client : Austrian industrial company
Period : 2018
Services : Risk analysis according to the checklist system, negotiations with authorities
The hazard assessment was necessary because the storage quantity of heavy heating oil in the cement plant exceeds the quantity threshold for petroleum products, which is defined as 2,500 Mg in column 2 of Part 2 of the List of Substances in Annex 6 to the AWG 2002. The hazard assessment was carried out according to the checklist procedure, which satisfies the requirements of §59a ff of the AWG2002 (Control of the hazards of serious accidents with Seveso substances).
After an inspection and local expert valuation of the plants, an existing hazard analysis was adapted to the current plant technology and to the state of the art and the current legal situation.
The system description and the safety assessment were presented in the form of a report and coordinated with the responsible official experts or authorities.
Nitrite reduction in the waste water of a steel processing company
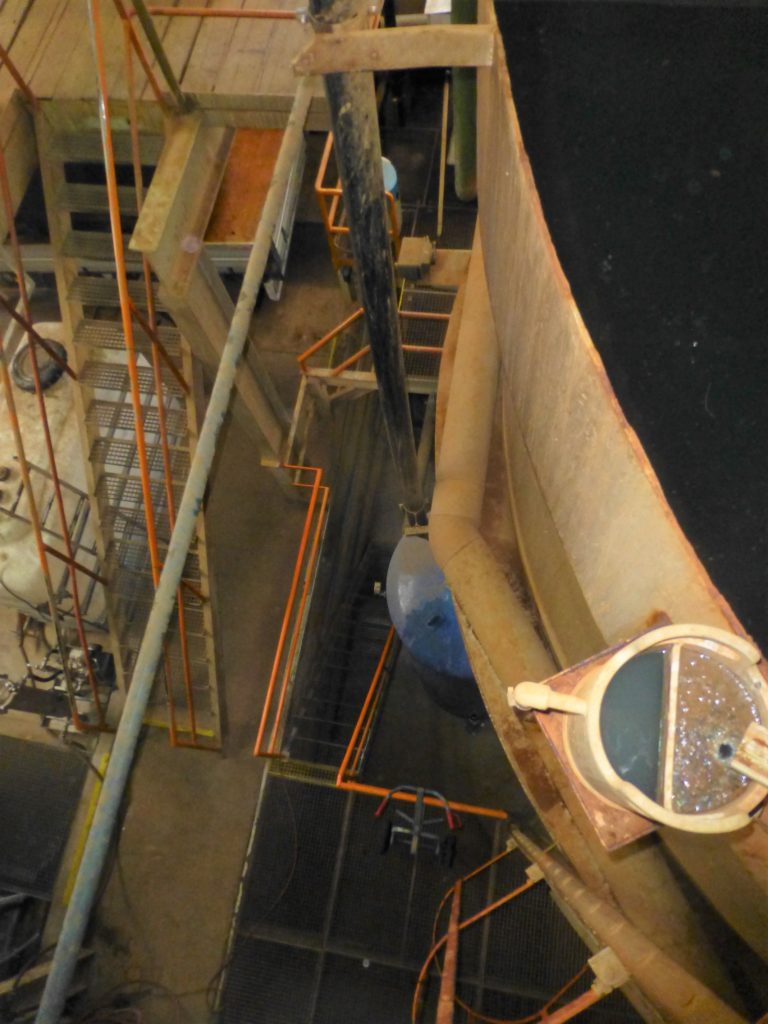
Client : Austrian industrial company
Period : 2018
Services : Inventory, definition and implementation of a measurement program to investigate the causes, optimization proposal
At the plant, the rinse water produced in operation is purified to direct discharge quality. The continuous neutralization consists of agitated tanks, a sludge settling tank and a chamber filter press for sludge dewatering. Elevated nitrite effluent values were measured in the pure water.
First, certain parameters at the various points of the wastewater treatment plant were analyzed by an authorized chemical laboratory. The environmental conditions (temperature, pH value, residence time, conductivity) in the sludge settling tank and the quantities of COD supplied by the condensate to an evaporator system favor the growth of microorganisms in the sludge. These convert nitrogen compounds into nitrite.
The following measures were taken: first, the bioactive sludge was completely removed from the system, then the condensate from the evaporator system was fed into the wastewater channel and the filtrate from the chamber filter press was no longer returned to the settling tank but discharged directly to prevent the accumulation of microorganisms. These measures immediately led to a stable nitrite concentration of less than 1 mg/l in the effluent.
Slaughterhouse - commercial license and indirect discharger approval
Client : Austrian engineering office
Period : 2018
Services : Advice on obtaining a new indirect discharger approval and the commercial permit
For a slaughterhouse, a technical pre-project planning was prepared on the basis of a local survey. For this purpose, plant construction, maintenance and disposal companies were contacted and the commercial license application was amended accordingly.
In the course of several on-site negotiations with the wastewater association, the indirect discharger consent of the regional sewerage company was also updated and, based on this, the renewal of the wastewater pretreatment system was designed on the basis of a modern chemically assisted flotation plant.
Food production - process and worker safety planning
Client : Austrian industrial company
Period : 2013
Services : Basic and detailed engineering of the process technology, approval procedures, tendering, employee protection issues
A Styrian food company produces a mechanically short-treated product from fresh produce, the treatment of which produces aggressive emissions. The employees must therefore be protected by innovative exhaust air collection measures and personal protective equipment.
In a first step, a functional design of the process technology and the mechanical equipment, including a plant flow diagram and a control and instrumentation diagram of the plant, was prepared.
The elaboration of specifications with regard to the pre-treatment and disposal of production wastewater, the treatment of emissions from exhaust air, the guarantee of the supply of unpolluted breathing air in the production process and a disposal concept for liquid and solid waste (waste management concept) represented further planning tasks.
Dedusting system for a secondary fuel plant
Client : Austrian engineering office
Period : 2008
Services : Detailed planning and documentation
On behalf of a large Austrian plant construction company, a new substitute fuel processing plant for a paper mill was designed together with an engineering firm. Our activities mainly covered the area of exhaust air technology. Through this project, the energy supply of the paper mill with alternative fuels was sustainably secured.
Bioethanol production using stillage in a biogas plant
Client : Austrian industrial company
Period : 2007-2008
Services : Basic engineering, submission planning
EnviCare ® prepared the submission plan for a bioethanol production unit and a fermentation residue processing unit as an addition to an existing biogas plant with 500 kW el .
The agricultural resources, corn and wheat grains, with a high dry matter content, are to be processed in the bioethanol plant. The bioethanol plant is designed to produce raw alcohol at 94 vol%. The entire plant consists of mash preparation, yeast preparation, fermentation process, carbonic acid washer, distillation and a steam generator. In addition, an extensive and membrane-supported digestate treatment plant was designed.
Tank interior cleaning Graz
Client : Austrian industrial company
Period : 2002-2004
Services : Basic engineering, submission planning
The tank cleaning plant is designed for the exterior cleaning of 33 trucks and for the interior washing of up to 16 tankers daily. Wastewater with excessive concentrations or concentrates are collected and handed over to authorised disposal companies, the rest is treated and discharged into the public sewer.
EnviCare ® was commissioned with the creation of the basic engineering and the official procedures for the commercial approval of the truck tank and exterior washing system.
Energetic optimization of a process plant
Client : Austrian industrial company
Period : 1998
Services : Creation of an energy concept
A disposal company operates facilities for the collection, interim storage and treatment of waste, operational wastewater and contaminated soil.
Waste oil, heating oil, electricity and natural gas are used as energy sources. Waste and heating oil are required for the operation of the plant technology and the associated heating system. The natural gas is used to heat the office wing. A load shedding system exists to optimise electricity consumption.
There are considerable heat losses while, on the other hand, the halls are additionally heated by the waste heat from the installed equipment. The hall ventilation was therefore to respectively be reduced to the required and officially prescribed level.
The operating plant could be optimised through improved output control of the steam boiler plant. Via control-technological optimisation the heating steam production was adjusted to the demand. Heating energy for the office building could also be taken from the condenser of the evaporator system. Energy costs were also reduced by adapting the load management concept.
Conformity assessment for an interlinked process plant (shredder)
Client : Austrian industrial company
Period : 1999
Services : Implementation of a conformity assessment with a checklist procedure
Since 1989, products placed on the market in Europe are required to be tested for conformity with the relevant EU directives and a CE marking must be affixed to these products. This also applies to deeply interlinked machines in their entirety.
In this specific case, the plant operator assembled various plant components, each of which had a valid CE marking, into a profoundly interlinked whole plant. He therefore had to carry out a conformity assessment procedure himself, in which we had to check compliance with the applicable guidelines and statutory regulations using a checklist procedure.
Safety analysis for a waste dump according to BGBL. 553/1991, 593 VO
Client : Austrian engineering office
Period : 1995
Services : Implementation of a safety analysis using a checklist procedure
The purpose of the safety analysis is to determine all relevant dangers that can emanate from the operating system.
A checklist procedure is used to split the facility into sub-facilities, which are classified by safety relevance. The relevant dangers are then determined for the individual, safety-related parts of the plant by starting out in tabular form from general sources of danger, which are related to the plant technology, to the accident event or environmental influences. The hazard source identification and the evaluation of the measures are recorded in tabular form.
Subsequently, the measures to control the sources of danger are listed and assigned to the identified sources of danger. In doing so, causal chains are taken into account. This is necessary in order to record those deviations from the intended operation that can lead to a malfunction condition only through the interaction of several conditions or events. The system parts that are important in terms of safety are to be determined.
Ultimately, each measure must be examined for its effectiveness, whether it could lead to the occurrence of a condition for the occurrence of an accident in accordance with the state of the art in safety technology.